Open Automatic Control System
CPBW FlexControl™
Drilling Fluid/Drilling Engineering Field Digital & Intelligent Service System—DFS
DFS Series Products
- Why choose DFS series products?
- Drilling Fluid/Drilling Engineering Field Digital & Intelligent Service System—DFS
- Laboratory Drilling Fluid Parameters Automatic Detection & Simulation Analysis System—DFSL
- Truck Mounted DFS System—DFSTM
- Related Subsystems of DFS Series Products
- AHT System
- IFS System
- VF&VPSS
- DFSMU
DFS Series Products
- Why choose DFS series products?
- DFS
- DFSL
- DFSTM
- Related Subsystems of DFS Series Products
- AHT System
- IFS System
- VF&VPSS
- DFSMU
Drilling Fluid/Drilling Engineering
Field Digital & Intelligent Service System—DFS

Drilling Fluid/Drilling Engineering Field Digital & Intelligent Service System—DFS

DFS System Data Output
Standard Function of DFS System
1
Applicable to Onshore & Offshore drilling field and meets ATEX Zone 2 Explosion-proof; Environmental adaptability temperature: -30~55℃;
2
Applicable Drilling Fluid (DF) : Water-based/Oil-based/Synthetic based/Solid-free DF (Excluding special DF for plugging);
● AV = 0~150MPa·S (Recommended Monitoring temperature of Water-based DF: 50℃ & Oil-based DF: 65℃); Temperature range: 10~80℃;
● Density = 0~3g/cm³, Output Frequency: every 5 minutes.
● AV = 0~150MPa·S (Recommended Monitoring temperature of Water-based DF: 50℃ & Oil-based DF: 65℃); Temperature range: 10~80℃;
● Density = 0~3g/cm³, Output Frequency: every 5 minutes.
3
Ability to directly acquire multiple data and present data/curve periodically (25~35 minutes); Automatic judgment of DF Flow Pattern (Bingham/Power Law/Heba/Carson);
4
With the function of Realtime Automatic pH Value Monitoring of Water-based DF and Realtime Automatic Electric Stability Monitoring of Oil-based DF;
5
Equipped with AHT System: Automatic API/HTHP (3.45MPa DP; 100/120/150/175/200°C) Filtration of Water-based DF & Mud Cake Thickness; Automatic Detection of Ca²⁺/Cl⁻ Concentration of API filtrate;
6
Equipped with RPCT (Remote Monitoring Portable Customer Terminal), with the ability to obtain real-time data of Mud Logging/Directional Well on site, realize Remote Monitoring + Digital Description of Wellbore Hydraulics While Drilling (Involving ECD & ESD, Borehole Cleaning & Cuttings Bed, Surge & Swab, Bit Hydraulics & Bit Selection Calculations, Sensitivity Analysis and Rheological Data of DF in Annulus While Drilling); Optimize/Recommend DEP; Critical Prompt/Alarm of real-time data/status; Digital Judgment/Analysis that provides decision support when dealing with complex situations;
7
Full Automatic/Unattended Operation Mode from "Start" to "Stop"; Self inspection after startup of detection unit; Automatic system process "Cleaning/Purging"; Self provided DF temperature real-time monitoring & closed-loop control system; Preset Self-start/Manual Random Start on site; Equipment Operation Fault Alarm; Setting/Alarm of real-time DF performance parameter "Safe Operation Window";
8
Have the ability to test small samples (at least 10L) of DF in the field, realize the rapid confirmation of DF slurry mixing/preparation parameters and the implementation, shorten the research & judgment/deployment time of DF, and systematically improve the field servicing efficiency of DF;
9
Data Transmission through Local Wired/Wireless Network (WITS0 Protocol, WITSML Format and TCP/IP Modbus Protocol);
10
DFSMMDR: DFS System Monitoring/Management Daily Report, which is used to record the report of DF/Drilling Engineering Site Events/Data;
11
Follow the guidelines of ANSI/API 13b-1/2 and GB/T 16783.1/2 Standards.;
12
According to JJG1002-2005 (National Metrological Verification Regulations of PR. China) and ANSI/API 13b-1/2, all DFS Series Products complete Calibration Operation of Rheological Verification with Confirmed & Standard Lube Oil before Ex-factory, and System itself automatically generates Digital Calibration Report based on each DFS Series Number.
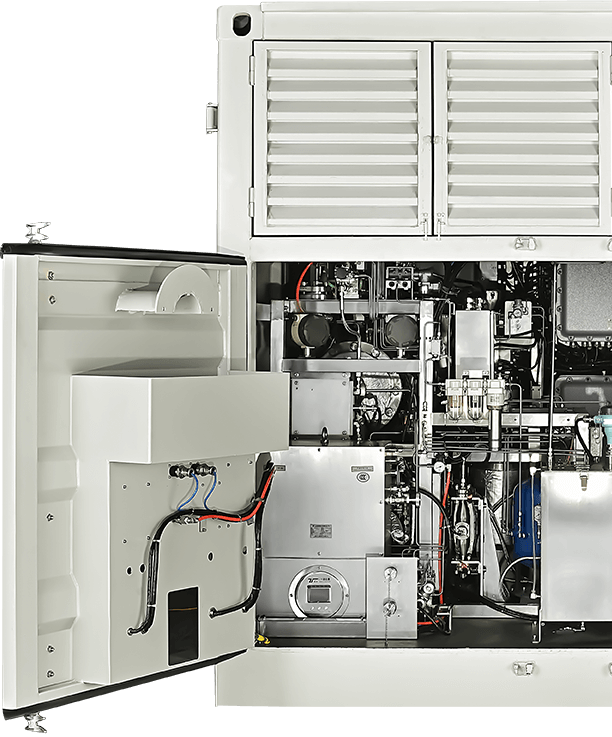
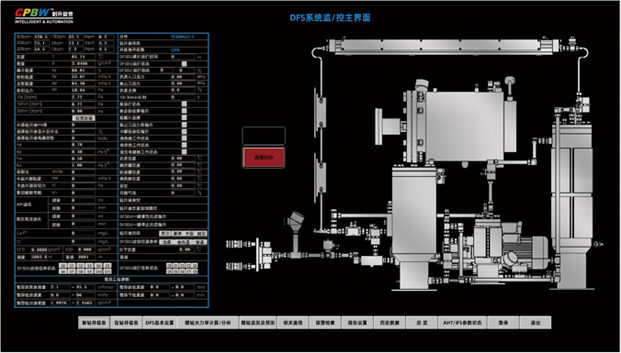
DFS System Standard Configuration Related Data Accuracy
1
Density: Nominal ACC.: ±0.002g/cm³; ACC. for DF: 0.005~0.01g/cm³;
2
Average Accuracy of Rheological Data output: ≥ 90%; Average Repeatability: ≥ 95%;
3
pH Value of Water-based DF: 0~14, ACC.: <0.3 drift;
4
AHT Subsystem: API Filtrate Volume (±0.1ml) & Mud Cake Thickness (±0.5mm)
5
Ca²⁺/Cl⁻Concentration of API filtrate:
Ca²⁺Concentration<400mg/L, error=40~80mg/L;
Ca²⁺Concentration>400mg/L, error<10%; Repeatability: >95%;
Cl⁻Concentration<1000 ppm, error=100~200ppm;
Cl⁻Concentration>1000 ppm, error<10%; Repeatability: >95%.
Ca²⁺Concentration<400mg/L, error=40~80mg/L;
Ca²⁺Concentration>400mg/L, error<10%; Repeatability: >95%;
Cl⁻Concentration<1000 ppm, error=100~200ppm;
Cl⁻Concentration>1000 ppm, error<10%; Repeatability: >95%.
Optional Function of DFS System
1
DF Dual Suction Circulation SYS realizes alternate monitoring & data comparison of DF performance by multi-point sampling in DF Solid Control SYS;
2
IFS SYS (Automatic Intermediate DF Feeding SYS), including tank, electric/gas/liquid/communication interface, pipe/cable, instrument, valve, PLC controller and Zone 1 EXP. Proof CERT. (Offshore/Standard Configuration; Onshore/Optional Configuration);
3
Hydrogen Sulfide Gas Alarm + Combustible Gas Alarm;
4
DERSS: Drilling Experts Remote Support SYS, Includes: RCT-S (Customer Network Server) & RCT-M (DERSS client) Software Deployment;
5
Realtime & Automatic Water/Oil Ratio for Oil-based DF. (0~20% Water in DF with ACC.: ±0.2%, Repeatability: ±0.1%);
6
Realtime Automatic detection of Suspended Solid Particle size and Suspended Solid Content (volume percentage) of DF; (Overall Measurement Range: 0.1~3,000μm; Solid Volume Concentration: 1~70%; Repeatability Error: <1% (Riffled Sample); Mean Relative Standard Deviation: <5%);
7
Electrical Power: AC 380V/50Hz+AC 460V/60Hz, 25KVA; Offshore: VF&VPSS (Variable Frequency & Voltage Power Supply Skid) (IP65); Onshore: DFSMU w/Built in VF&VPS (Variable Frequency & Voltage Power Supply);
8
DFSMU:Monitoring/Man-machine Workstation with remote monitoring, data analysis/calculation functions, which is located in Safe Area of drilling field; Dimension: L3.40m * W2.47m * H2.44m; Includes: Power Supply Interface (AC 220V/50Hz & AC 110V/60Hz), A/C & Electric Heating, Lighting, Industrial Embedded Host & Display (RCT, Remote Customer Terminal), Wireless Communication Port, Wireless Keyboard/Mouse, Wired Network Interface, Workbench/Chair, Filing/Storage Cabinet.
9
Notes:
● Above 8 Optional Functions operate based on the existence of standard configuration, customer can choose based on standard configuration of DFS System;
● There is no causal and interdependent relationship between above 8 Optional Functions.
● Above 8 Optional Functions operate based on the existence of standard configuration, customer can choose based on standard configuration of DFS System;
● There is no causal and interdependent relationship between above 8 Optional Functions.
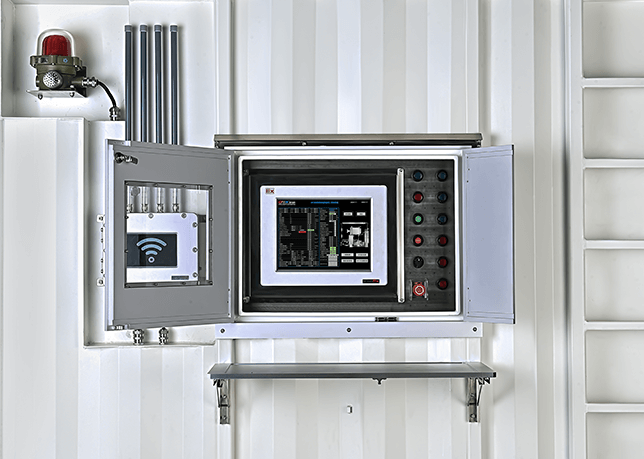
DFS System Composition & Field Layout
DFS System Data Capability
Drilling Fluid / Drilling Engineering Field / Realtime / Dynamic Data Calculation / Analysis
Business Value of DFS System Application
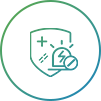
Avoid Kick/Lost Circulation/Sticking caused by DF to the greatest extent;
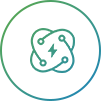
Apply Digital/Intelligent means to improve Real-time Prevention & Control Ability of DF Well Control;
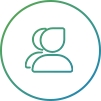
Systematically reduce 30% or more NPT caused by DF and Operation Personnel Investment;
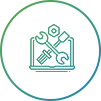
Improve the scientificity, timeliness and compliance of DF/Drilling Engineering Implementation, Supervision and Management in drilling field;
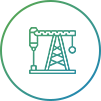
A new breakthrough of Rigid Demands about Technologies/Products in the field of DF, promote Comprehensive Digital Transformation of Drilling Engineering Field and Obtain the sustainable results of “Quality Improvement/Cost Reduction/Efficiency Increase" (QI/CR/EI) at the engineering level.
Development History of DFS System

2018.12
CPBW launched the first generation DFS system in December, 2018.
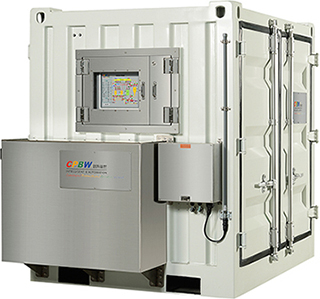
2019.05
CPBW took First Generation DFS system to participate in OTC exhibition in Houston, USA in May, 2019.
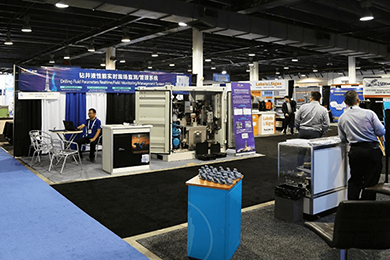
2020.07
The second generation DFS system was tested/verified in ChangNing shale gas well Ning 209h27-2/Ning 209h27-3 of PetroChina in July, 2020.
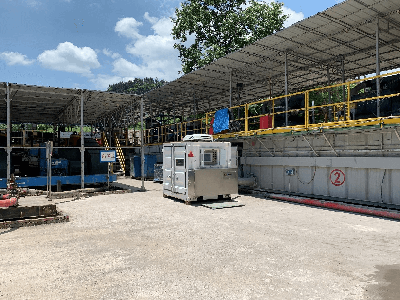
2021.07
The second generation DFS system was tested/verified in FuLing JiaoYe well 107-7HF of Sinopec in July, 2021
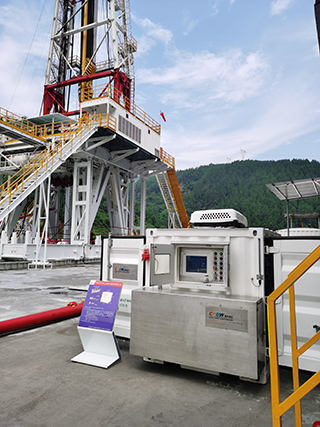
2019.01
The first generation DFS system was tested for the first time in WeiYuan shale gas drilling field, Sichuan, China in January, 2019.
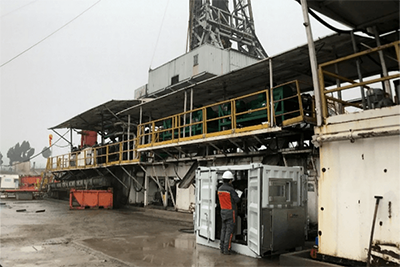
2019.11
CPBW launched the second generation DFS system in November, 2019.
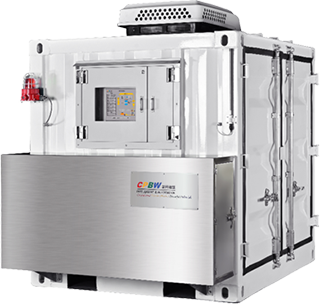
2020.12
The second generation DFS system has been tested/verified on COSL 937 platform in December, 2020.
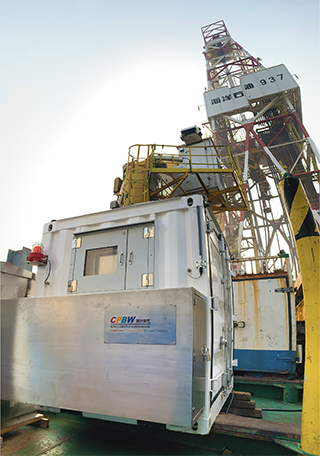
2022.03
CPBW launched the third generation DFS system in March, 2022.
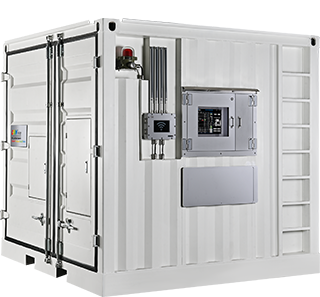
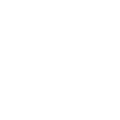